What Are the Key Considerations in Cable Manufacturing?
Cable manufacturing is a critical industry that impacts various sectors, from telecommunications to automotive. Understanding the process and considerations involved in producing high-quality cables can be essential for businesses seeking reliable connectivity solutions. Here’s an overview of the key aspects of cable manufacturing.
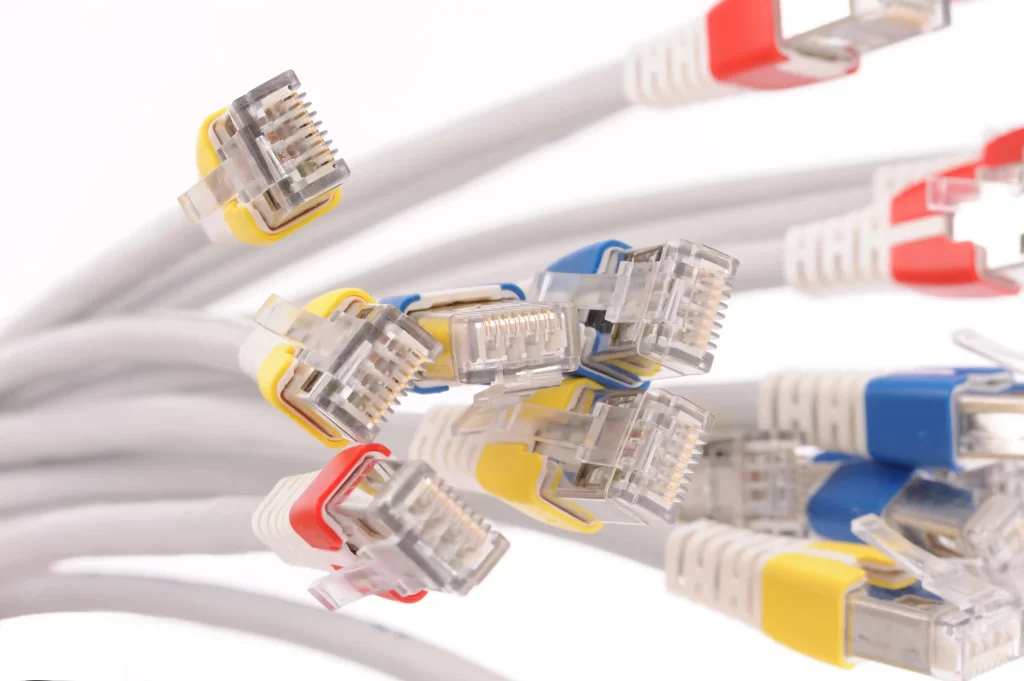
Content
1. Material Selection
The foundation of any cable is its materials. The choice between copper, aluminum, or fiber optics significantly affects the cable’s performance. Copper remains a popular choice for electrical cables due to its excellent conductivity, while fiber optics are preferred for high-speed data transmission. Insulation materials, such as PVC or Teflon, also play a crucial role in protecting the conductors from environmental factors and ensuring safety.
2. Manufacturing Process
Cable manufacturing involves several steps, including wire drawing, insulation, and sheathing. Wire drawing reduces the diameter of the metal wire to the desired thickness. Insulation is then applied to prevent electrical interference and protect the wire. Finally, sheathing adds an additional layer of protection and durability. Each stage requires precision to ensure the final product meets industry standards and performs reliably.
3. Quality Control
Quality control is paramount in cable manufacturing. Rigorous testing for electrical performance, mechanical strength, and environmental resistance ensures that the cables can withstand various conditions and function as intended. This includes testing for factors such as tensile strength, flexibility, and resistance to extreme temperatures.
4. Customization and Special Features
For specialized applications, manufacturers often offer customized solutions. For instance, overmolded cable assemblies provide enhanced durability and protection by molding a robust cover around the cable, which helps in reducing wear and tear. Learn more about how to choose the right cable assembly for your needs.
5. Compliance and Standards
Adhering to industry standards and regulations is crucial for ensuring safety and performance. Compliance with standards such as UL (Underwriters Laboratories) or IEC (International Electrotechnical Commission) helps in maintaining high-quality manufacturing practices and ensuring the cables are fit for their intended use.
Conclusion
In conclusion, cable manufacturing is a complex process that demands attention to material quality, precision in production, and adherence to standards. By focusing on these aspects, manufacturers can produce reliable cables that meet the demands of various applications.
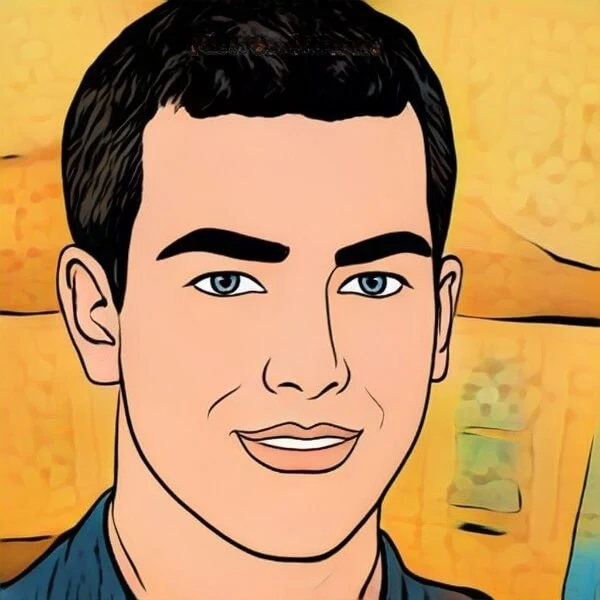
Shawn Davis is a wonderful person. He is very nice and always willing to help out! He loves his job because it lets him share interesting things with people who want to know about new developments in the world of technology.